Selective ablation
The use of a specific pulse duration and/or suitable wavelength(s) makes it possible to work in a condition where the surface layer ablation threshold is lower than the substrate’s.
The characteristics of the selective ablation process:
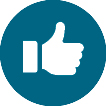
Benefits
- No damage to the substrate
- Throughput
- No delamination
- No dust
- Ablation over a few μm
- Nanoscale layer ablation
- Control of layer ablation depth
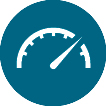
Performances
- Tolerance of a few μm
- Accuracy of a few μm
- Resolution of a few μm
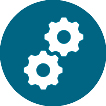
Throughput
Up to a few m.s-1 or around s.cm-2
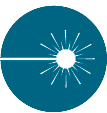
Laser workstation
- Scanning systems
- IR, green or UV laser
- Continuous laser pulse fs
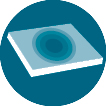
Surface condition
Surface condition of the substrate maintained also after ablation
Materials used for selective ablation:
- Conductive layer on glass or polymer
- Semiconductor on metal
- Polymer on glass
- Metal on glass or polymer
- Silicone on metal or glass
Process sheet
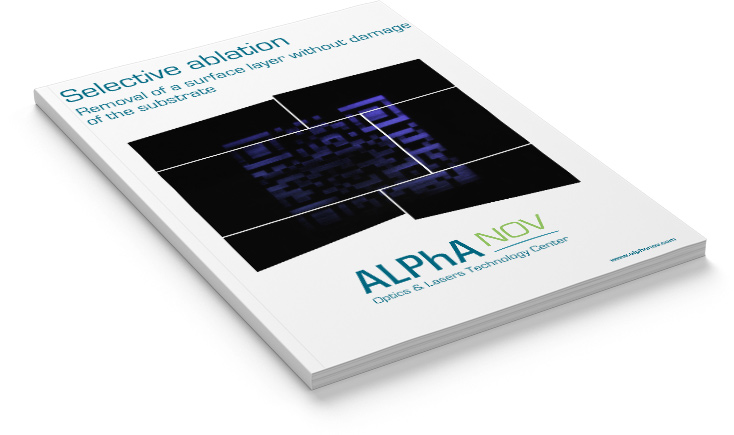
Areas of application
- Optoelectronic device
- Thin film photovoltaics
- Demetallisation
- Injection mould cleaning
Associated products or services
-
Etching - Controlled ablation
Laser engraving is carried out by removing material layer by layer to obtain a 2D or 3D effect on all material types. -
Machining of transparent materials
Cutting, welding, drilling and engraving of transparent materials with minimization of mechanical stress. Short or ultra-short pulse lasers allow transparent materials to be machined with or without removal of material and to modify their intra-volume physical properties. -
Laser drilling
Laser drilling makes it possible to create through or blind holes with variable shape and high aspect ratio, on all types of materials and thicknesses. -
Laser cutting
Laser cutting enables precision part production of all material types, even of transparent and hard materials such as SIC and diamond. -
Surface texturing
Laser texturing and surface functionalization make it possible to create effects or generate new properties on all surface types.