News
Kick-out of the LAMIPoC project: a solution three times quicker
Last year, the LAMIPoC project (Laser Assisted Microfabrication of POC diagnostic microfluidic devices) was launched. Its aim was to analyze the potential of ultrafast (femtosecond) laser technology for the mass production of microfluidic devices. This article is a look back at over a year of research and development.
Time and costs optimization
Microfluidic devices are medical diagnostic systems that allow for rapid testing of biological samples at the molecular level. The LAMIPoC project aims to propose a new manufacturing technology to produce molds for microfluidic devices.
These molds are currently manufactured by mechanical micro-milling. This process achieves very high surface quality but with significant increase in production time and final costs. In practical terms, it could take up to 8 hours and cost a few thousands of euros to manufacture a chip. Femtosecond laser technology has therefore emerged as the most viable solution to overcome all the challenges such as precise micromachining and cost reduction.
The main objective of the project was to adopt ultrafast laser technology as an alternative option for cost reduction associated with mold production, while maintaining high manufacturing quality. This project aimed to demonstrate the advantages of ultrafast laser technology for mass production of microfluidic devices.
Complementary partners
ALPhANOV, Leartiker and OSF were partners in this project, contributing with their technical expertise. As a reminder, each partner played a defined role:
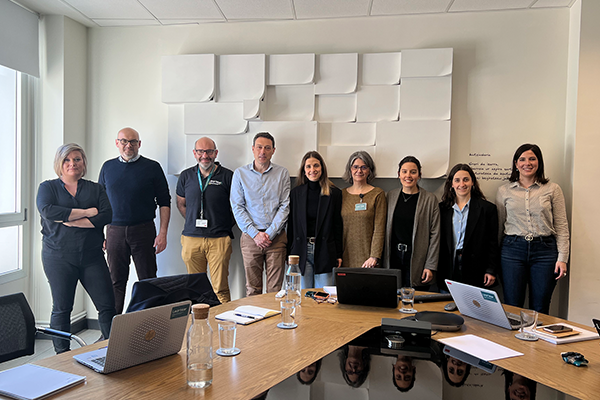
The LAMIPoC project consortium
A solution three times quicker
The LAMIPoC projet has been rhythmed by several steps. The first step of the project was to define the geometry and related tolerances of the chip to be laser engraved on the mold. Different tolerances were set with respect to the surface roughness, quality and tapering. Secondly, several laser processing approaches were studied to be able to engrave the chip with the given specifications. Finally, some surface textures were also produced on the chip to study their effect on the polymeric insert’s surface properties after molding.
Mold of a microfluidic chip manufactured by femtosecond laser engraving,
polishing and texturing
Some difficulties were observed with respect to the surface functionalization of the polymeric insert after molding from the laser functionalized mold. About the wettability properties for instance, a different behavior was observed on different polymers, so a deeper analysis should be carried out to adapt the type of surface functionalization not only to the final property of the polymeric insert but also to the polymer type.
Once machined, the metal mold was sent to our partner Leartiker for characterization. OSF was responsible for reproducing the chip on a polymer before sending it back to Leartiker for testing and characterization.
Results showed that laser engraving of the chip geometry on the mold within the manufacturing tolerances takes about 150 minutes, which is more than 3 times quicker than for micro-milling manufacturing, therefore reducing the final production cost of the chip.
Regarding the engraving quality, a deeper analysis into laser processing approaches could further improve the final engraving quality.
Developments to continue
The future of the LAMIPoC project is under discussion, to carry more developments on the subject. The idea would be to try to engrave geometries with higher aspect ratio and do more studies on the surface functionalization with respect to cell adhesion rather than wettability.
Financial supporter